
- Antilock Braking system
- Sterling Engine
- ISO standard 9001 (ws)
- Bearing failure
- Geo-exchange heat pump
- Ship stabilization
- Solar pump
- Hydrostatic Journal Bearing
- Regenerative Braking System
- Six Sigma (ws)
- Rolling mill
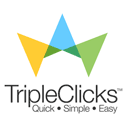
A rolling mill is a machine or factory for shaping metal by passing it between a pair of work rolls.
Rolling mills are often incorporated into integrated steelworks, but also exist as separate plants and can be used for other metals, and other materials.
Rolling mills historically have been of several kinds:
For silversmithing mainly two types are used, a flat one (with two cylindrical rolls) for rolling sheet and one with grooved rolls for rolling octagonal wire. The rolls are made of hardened steel.
Six sigma is a set of methodologies used by businesses to achieve extremely low failure rates in any process. The term six sigma derives from the mathematical use of sigma in statistics as a standard deviation. Six sigma is therefore six standard deviations.
In theory, a six sigma would be approximately two failures per billion attempts. In practice, due to a drift of plus or minus 1.5, six sigma status means less than 3.4 failures per million. This is an extremely low rate of failure, but has been proven possible in industry after industry over the past twenty years.
Bob Galvin of Motorola was a trailblazer in the adoption of six sigma by Motorola and other companies. His insistence on high levels of quality control, and subsequent vindication as Motorola achieved these levels, led to the spread of the six sigma system throughout the manufacturing world. The tenets of six sigma have since been successfully applied in many other areas of business, including customer service, transactional businesses, and the service industries.
The term failure is defined within each industry and product line, and simply means a defect that customers consider critical. Six sigma attempts to reduce these defects to a level below 3.4 failures per million.
There are two main methodologies in six sigma. The first is the DMAIC process: define, measure, analyze, improve, control. The second is the DMADV process: define, measure, analyze, design, verify. DMAIC is used for processes already in place which do not meet six sigma specifications, to help bring them within the six sigma threshold. DMADV is used for the development of new products or processes, to ensure that they meet the world at six sigma levels of quality.
There are three main certification levels of six sigma mastery: six sigma green belts, black belts, and master black belts. To achieve each ranking, one must undergo extensive training in six sigma techniques and methodologies, then pass a certification test. According to some research, six sigma black belts save companies an average of US$200,000 to US$300,000 per project and are able to complete up to six projects per year.
General Electric is the poster-child of the six sigma movement, with estimated savings of over US$10 billion within the first five years of implementation since 1995. Their dedication towards reducing variation on each and every transaction since implementation has led not only to increased profits, but also to an improved public image and customer relations.
Six sigma values are straight-forward and incredibly useful for businesses of all sizes. By focusing relentlessly on quality and the reduction in variations of product consistency, six sigma promises a better business overall........
Regenerative braking is used on hybrid gas/electric automobiles to recoup some of the energy lost during stopping. This energy is saved in a storage battery and used later to power the motor whenever the car is in electric mode.
Understanding how regenerative braking works may require a brief look at the system it replaces. Conventional braking systems use friction to counteract the forward momentum of a moving car. As the brake pads rub against the wheels (or a disc connected to the axle), excessive heat energy is also created. This heat energy dissipates into the air, wasting up to 30% of the car's generated power. Over time, this cycle of friction and wasted heat energy reduces the car's fuel efficiency. More energy from the engine is required to replace the energy lost by braking.
Hybrid gas/electric automobiles now use a completely different method of braking at slower speeds. While hybrid cars still use conventional brake pads at highway speeds, electric motors help the car brake during stop-and-go driving. As the driver applies the brakes through a conventional pedal, the electric motors reverse direction. The torque created by this reversal counteracts the forward momentum and eventually stops the car.
But regenerative braking does more than simply stop the car. Electric motors and electric generators (such as a car's alternator) are essentially two sides of the same technology. Both use magnetic fields and coiled wires, but in different configurations. Regenerative braking systems take advantage of this duality. Whenever the electric motor of a hybrid car begins to reverse direction, it becomes an electric generator or dynamo. This generated electricity is fed into a chemical storage battery and used later to power the car at city speeds.
Regenerative braking takes energy normally wasted during braking and turns it into usable energy. It is not, however, a perpetual motion machine. Energy is still lost through friction with the road surface and other drains on the system. The energy collected during braking does not restore all the energy lost during driving. It does improve energy efficiency and assist the main alternator......
Typical solar water pump applications:
Hello friends!! Here You will get necessary information to make seminar on any mechanical topics and it's totally free.